現代制造業對"小批量、多批次"生產模式的需求,推動著機器視覺系統從單一檢測工具向柔性生產中樞演變。在產品質量檢測環節,傳統AOI設備受限于預設規則的剛性框架,難以應對新型缺陷的識別挑戰?;谏疃葘W習的視覺系統通過構建多層卷積神經網絡,在每當發現未知缺陷特征,會自動生成標注任務流,形成"發現問題-學習特征-預防風險"的產品質量閉環管理。
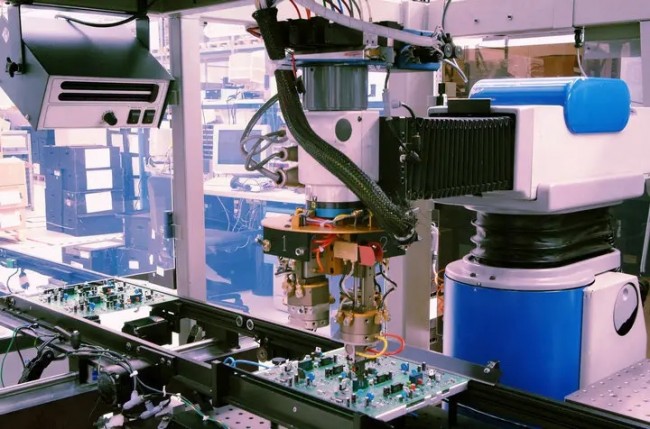
深圳虛數將將DLIA工業視覺系統與某汽車零部件工廠的MES、ERP系統深度集成,構建起跨維度的質量追溯體系。當視覺終端捕捉到變速箱殼體毛刺超標時,不僅觸發即時分揀指令,同時將工藝參數偏差同步推送至加工中心,在30秒內完成刀具補償參數的自動修正,將質量管控從末端攔截轉變為過程干預,缺陷攔截節點平均移至前個工序段。
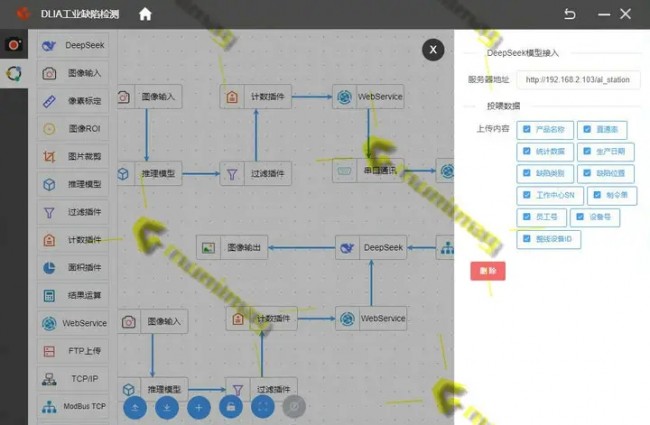
在機器視覺與人工智能的協同作用下,工廠正演變為具備神經反射弧的有機體。當視覺傳感器捕捉到注塑件縮痕時,DLIA工業視覺系統不僅追溯模具溫度曲線,還會聯動供應鏈系統分析原料批次特性。通過實踐表明,這種跨系統協同可提升不良品根本原因分析效率。更深遠的影響在于,持續積累的視覺數據正在訓練出行業級的知識圖譜,使制造系統獲得類似"經驗直覺"的決策能力——當檢測到新型材料表面波紋時,能自動匹配歷史數據庫中的相似案例的工藝調整方案。
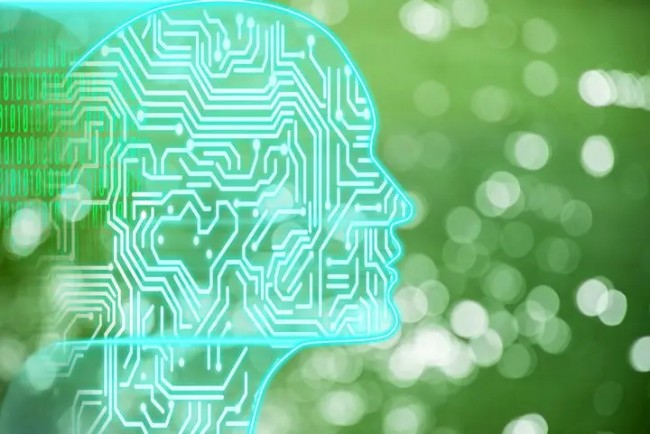